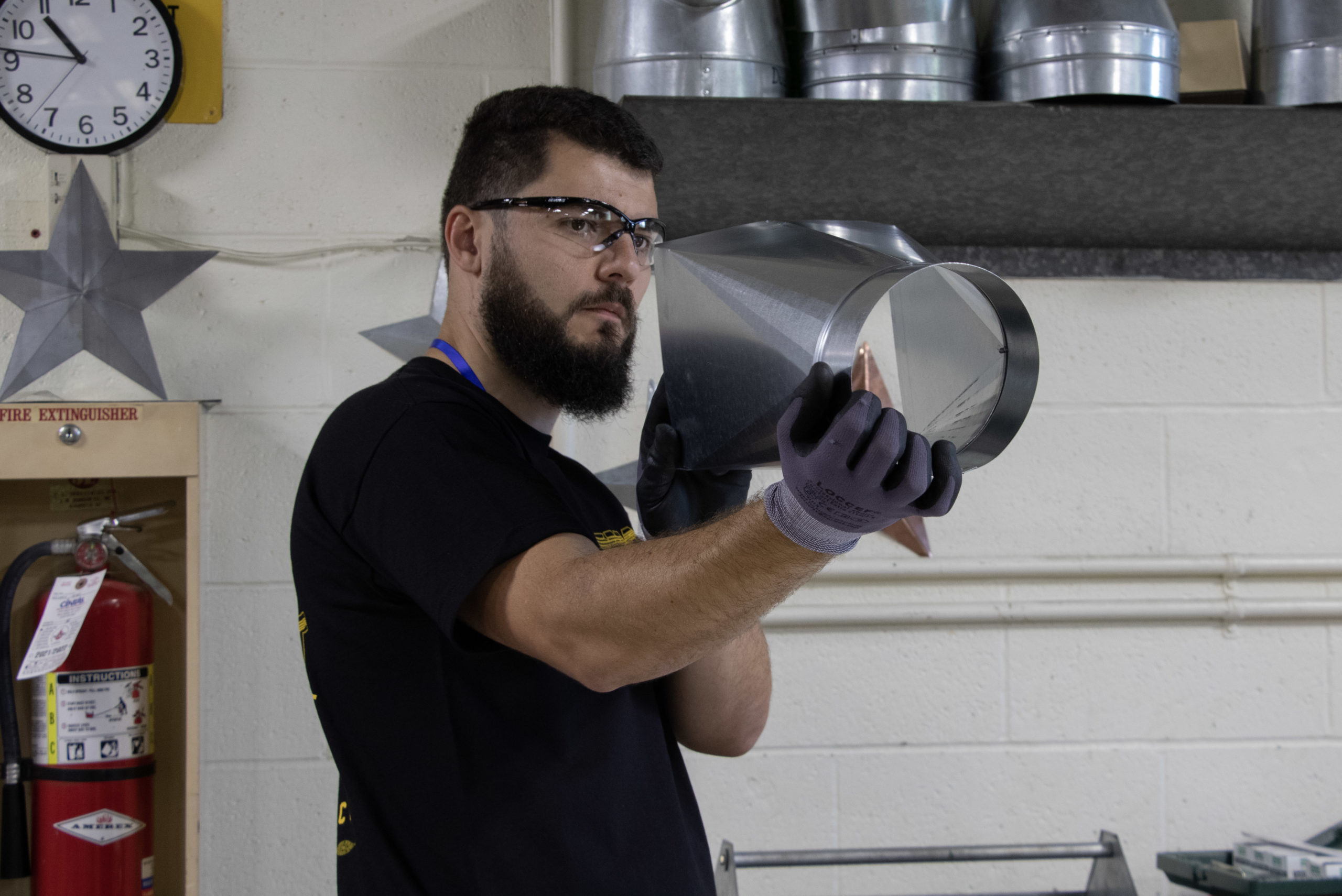
Sheet metal fabrication is a vital industry that bridges creativity, precision, and practicality. Georg Hoefer, a Local 19 fourth-year apprentice, has had the unique opportunity to work in both Germany and the United States, offering a fascinating perspective on the key differences and similarities between these two countries’ approaches to this craft.
Advanced Automation vs. Attention to Detail
One of the most noticeable differences Georg experienced was the level of automation in sheet metal shops in Germany compared to the U.S. In Germany, he worked in a modernized shop where machines were highly automated, even featuring a robot to load and unload materials. This level of automation streamlined processes and improved efficiency, allowing for the fabrication of a wide range of materials. Notably, Georg and his colleagues had to work with a variety of grades of steel, aluminum, and stainless steel, catering to specific customer requirements. This need for diverse materials in Germany fostered a culture of accuracy and precision to ensure the quality of the final product.
Metric vs. Imperial Systems
Another stark difference was the use of the metric system in Germany, which Georg found to be more accurate and easier to work with compared to the imperial system used in the U.S. The metric system’s consistency and simplicity made measurements and conversions more seamless. However, Georg found that his experience with fractions from middle school education helped him adapt to the U.S. system.
Safety and Standards
Georg observed similar safety rules in both countries, with an emphasis on the employer’s responsibility for the safety of the workplace. However, in Germany, the Berufsgenossenschaft (employer’s liability insurance) played a significant role in enforcing safety standards and providing compensation for work-related accidents.
When it comes to quality assurance and standards, Georg noted that Germany’s sheet metal industry demands higher levels of accuracy due to specialized applications. The use of ISO standards and precise measurements ensures a consistent quality level that meets customers’ stringent requirements.
Materials and Techniques
Georg pointed out the difference in materials used between the two countries, with the U.S. relying more on galvanized sheets and Germany working extensively with black iron, stainless steel, and aluminum. Georg’s experience with fabricating aircraft parts in Germany required him to work with a wider variety of materials, each with specific properties tailored for their application.
Basic machinery like press brakes, power rolls, and power shears are the same in both countries. Welding techniques and equipment are the same as well.
In terms of fabrication techniques, Georg found laser cutting to be more efficient than plasma cutting but acknowledged that laser cutters were costlier. CNC press brakes, he explained, were crucial for achieving high accuracy and efficiency, especially when dealing with repetitive patterns in sheet metal. Georg’s experience in Germany with specialized machinery, such as a fully automated laser plant with robotic material handling, allowed for greater versatility in manufacturing.
Quality Control and Communication
Quality control played a significant role in both countries, with Georg’s German experience involving meticulous documentation and measurement. This attention to detail ensured customer satisfaction and the production of accurate components. Communication and collaboration within the workplace were essential to rectify mistakes and prevent future errors, regardless of whether Georg was working as a quality inspector or fabricating parts himself.
Although Georg’s experiences in Germany were in the sheet metal industry, differences in the type of manufacturing are evident. The overall skill set from both countries requires sheet metal workers to pay attention to detail and have pride in their work.
“Making the move to the United States from Germany was a big leap, but one that was worth it. While I miss my loved ones back home in Germany, I am so thankful to my Local 19 brothers and sisters who have helped me feel at home in America as I continue to grow my skills here,” said Georg.
Georg Hoefer’s journey in the sheet metal industry provides a captivating insight into the nuances and distinctions between the two countries’ approaches to the craft. From advanced automation and material variety in Germany to a focus on safety standards and quality assurance, the sheet metal world evolves in unique ways across different cultures. Local 19 has been proud to welcome Georg into our union family. Georg’s experiences underline the importance of both precision and adaptability, showcasing the shared passion for craftsmanship that transcends borders.